A New Method With Ceramic Can Help Electronics Manufacturing
Viswamitra Jayavant - Sep 27, 2019
Researchers have found a new method with which they can deal with ceramic: By firing short-pulse laser at them until they weld into one another.
- This App Helps You Fix Electronics In Seconds, You Just Need To Scan
- The Government Announced Rs 36,000 Crore Fund To Boost Local Manufacturing
- This Drone-Vacuum Flies From One Floor To Another
Although most people associate ceramics with pottery and fine china, it also has a vast number of other usages. For example, in modern day’s electronics, ceramic is a crucial ingredient in creating capacitors, resistors, inductors among other things that had more or less made smart devices feasible. They’re also bio-compatible, which makes them the perfect material for bio-implants.
That’s the reason why researchers have been hard at work trying to find different manufacturing processes for ceramic that could make it more useful.
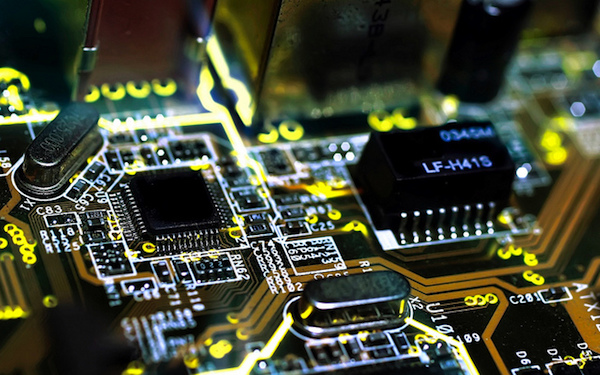
The latest development in the entire effort came from a group of American engineers who discovered a welding technique that can expand the application of ceramics broader than ever before. Technically, the idea revolves around a laser beam that pulses at an ultrafast frequency to melt ceramic sheets at their interface and combine them together.
The great thing about this technique is that, according to the engineers, it not only works at room temperature, humidity, and pressure, but it also uses a relatively efficient laser power at 50 watts. Traditional methods require the ceramic parts to be pre-heated in a specialized furnace, so this is more practical and ultimately, cheaper for manufacturing.
The Two Problems of Ceramic Making
But what this means for electronics manufacturing is far more than providing a cheap production process. Right now, according to Javier Garay, the senior author behind the project, because traditional methods require ceramics to go through a furnace at high temperature, it’s extremely difficult to put ceramics inside the casing of a device and put the entire thing through the furnace. The electronics would melt inside, rendering it unusable.
A second challenge is an inherent difficulty in welding ceramics together. Ceramics often have a very high melting point, so subjecting them to such temperature can make them crack.
Laser Welding
To solve this problem, they utilize a series of ultrafast laser pulses along with the interface between two sheets or parts made out of ceramic. This can ensure that the high temperature from the laser would be centralized only at the point of welding, causing localized melting of the material.
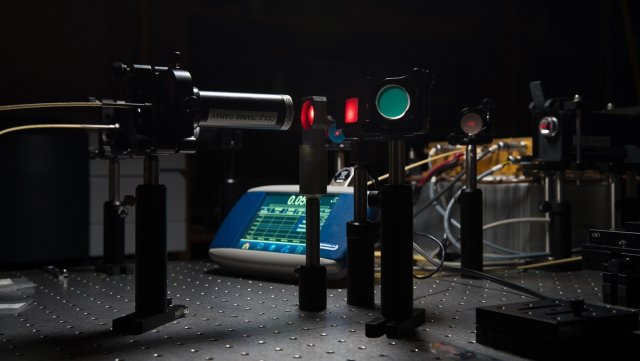
But this doesn’t mean that the entire operation is simple, the researchers have had to take into account a lot of different values. From the transparency of the material itself to the properties of the laser they wanted to blast it with: The exposure time, number, and the duration of each pulse. If they managed to optimize these values, they could find just the correct ‘spot’ in the algorithm to maximize the melt diameter, reduce the ablation of the material, as well as having an accurate cooling time for a good weld.
Huge Implication
In order to prove the feasibility of their method, the researchers welded a transparent, cylindrical cap to the innards of a tube made out of ceramic. After testing the welds, the result came back spectacularly: The welds are actually sturdy enough to hold a vacuum. A vacuum test, according to the lead author Elias Penilla, is the standardized testing method in the electronics industry to test the seals on anything ranging from consumer-grade electronics to highly sophisticated optoelectronic instruments.
The laser welding technique shows quite a lot of potential, but at the moment, the researchers are still starting out slow: They’re welding together objects that are only some 2 centimeters in size. Of course, as with any prospective industrial processes, they’re trying to find ways to scale it all up.
Featured Stories
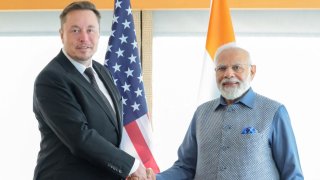
Features - Feb 26, 2025
Elon Musk Eyes Indian Market: Tesla’s Next Big Move?
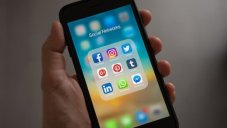
Features - Aug 03, 2023
The Impact of Social Media on Online Sports Betting
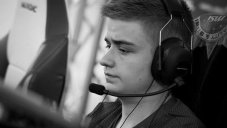
Features - Jul 10, 2023
5 Most Richest Esports Players of All Time
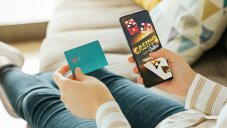
Features - Jun 07, 2023
Is it safe to use a debit card for online gambling?
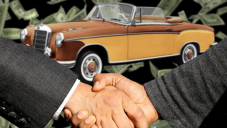
Features - May 20, 2023
Everything You Need to Know About the Wisconsin Car Bill of Sale
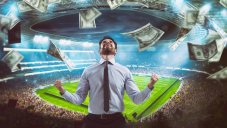
Features - Apr 27, 2023
How to Take Advantage of Guarantee Cashback in Online Bets
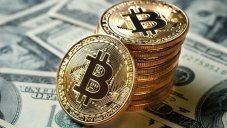
Features - Mar 08, 2023
White Label Solutions for Forex
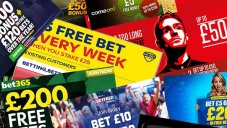
Review - Jul 15, 2022
WHY BETTING SIGNUP OFFERS ARE IMPORTANT FOR NEW GAMBLERS
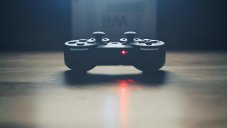
Mobile - Jul 01, 2022
The Best Sports Video Games to Play in 2022
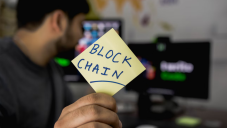
Features - Apr 28, 2022
0 Comments
Sort by Newest | Popular