Manufacturing Sectors In India Are Quickly Swifting To Automation
Arnav Dhar - May 20, 2019
With the technology advance of Industry 4.0, India's manufacturing area is changing swiftly thanks to the applications of automation.
- Delhi Is The World’s Most Polluted Capital City For Three Years In A Row
- Indian Farmers Install High-Tech, Night-Vision CCTV Cameras To Protect Themselves
- Looking For The Best Electric Bike In India 2021? Take A Look At These
With the technology advance of Industry 4.0, India's manufacturing area is changing swiftly. It is understandable that to keep being competitive and well-developed, the factories across the country are becoming smarter and more productive thanks to automation.
Take Thermax's new plant at Dahej, Gujarat, for instance. The firm had a staff cutback in its chemical processes which involved ion-exchange resin and create dedicated algorithms for the whole process. The system is fed with the designated formulas and procedures. The chemicals will then be released from their tanks on top of the five-story structure. When they are poured down, the steamers and chillers below will then be ready to work with the programmed pressure and temperature.
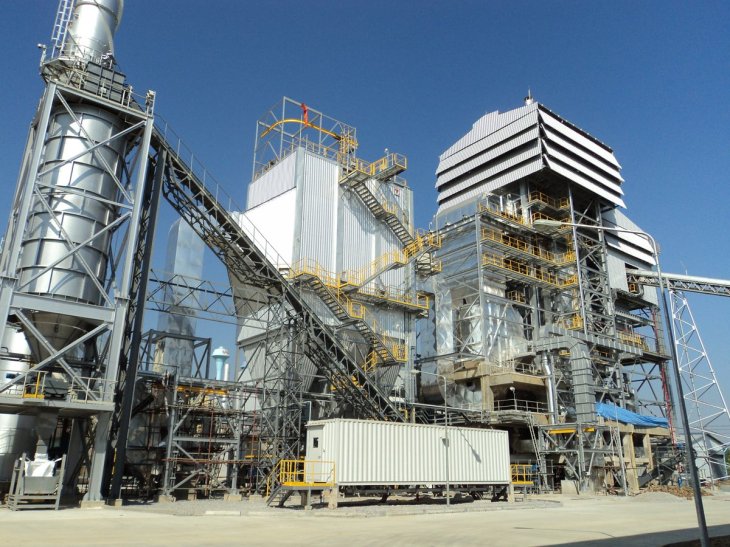
According to Thermax's managing director Unnikrishnan, it was "tough" to create all the algorithms in order to automate an used-to-be-manual process.
Thanks to automation, Thermax' new Sri City-based factory is advanced enough to reduce an original 40-day-long production process to a 15-day-long one. It is trying to automate its other 13 factories, a part of which is now as old as 40 years.
Estimations show that the whole of India's automation market is worth $2 billion. However, the levels of automation are different from sector to sector.
The manufacturers of the consumer goods have started to integrate IoT into their processes, they have also brought robots to the shop floor.
Automakers are using AR and VR in training employees, especially those who are working in sophisticated producing steps.
Other sectors are witnessing production drawings replaced with handheld devices, which helps minimize the risk of errors. 3D printers have been brought in too.
Larsen & Toubro, an engineering giant, is also automating its manufacturing process in both construction sites and shop floors. For example, an used-to-manual process like welding is now automated and monitored by an operator via consoles. According to the company's CDO Anantha Sayana, this improvement in technology helps enhance the work's quality and help the workers have a better working environment.
Starting in 2016, L&T digitalized its construction sector, which worthed 60% of it. Since then, 9,600 pieces of equipment from more than 400 construction sites have been connected and installed with gateways and sensors. These sensors are said to create a huge amount of data, but to ensure that it works flawlessly with better security and is easier to use and control, they integrated both IT and OT.

Hosur-based cab panel pressing factory of Ashok Leyland was also automated lately. The original presses and dies processes were improved with automation. Thanks to the improvements, its productivity soon doubled.
According to Harihar P, the company's VP:
The whole process now ensures perfect quality for the products. The factories of automaker M&M, which used to be only manual, are now occupied 70% by the robots. CEO Vijay Kalra highlighted the importance of adopting technology in manufacturing by saying it is "critical". He also noted that those who work on the technology "should be well-versed with it."
Unity Technologies India's Anumukonda Ramesh said that the auto industry is quickly prototyping some AR/VR and 3D solutions.
Reliance Industries is another giant interested in VR since it finds the tech helpful for employees training and in safety tests for productions. The company said in its last year's annual report that 3D printing would play an important role in its digital manufacturing architecture. The report stated:
Currently, most companies are using their internal teams for designing and shifting to automation, partnerships with vendors and startups are for the actual tech. Sayana from L&T highlighted this while saying that the techs and platforms are always available, so the remaining of the works is kept internal, not to mention group companies can always share services and expertise.

Yet the automation hasn't been easy.
While shifting to an automation player, Mahindra's Kalra expressed that they faced many difficulties when it particularly comes to IT infrastructure, skills gap, and equipment's compatibility.
Other worries which slow the automation process include difficulties in upgrading inherent systems with new techs and cooperation weaknesses in the value chains.
Technological upgrades will never reach their full potential given that the whole ecosystem of firms, suppliers, and companies can't work together and instead follow individual interests, according to a member from Protivity.
The challenges exist, yet automation is a manifest trend, as the tech giants are urgently following the process.
It is proven that the tracking systems on input materials in Thermax's and L&T's factories are working effectively to provide better knowledge for manufacturing as well as eliminating rates of wastage.
For now, investing in new 4.0 techs seems to be soaringly expensive, but in the long run, it is promising that companies will save more costs if they choose to follow an up-to-date, suitable process.
Featured Stories
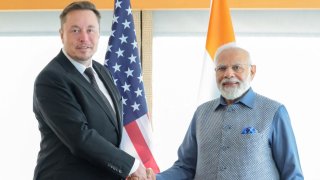
Features - Feb 26, 2025
Elon Musk Eyes Indian Market: Tesla’s Next Big Move?
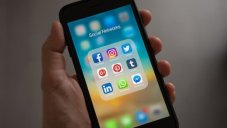
Features - Aug 03, 2023
The Impact of Social Media on Online Sports Betting
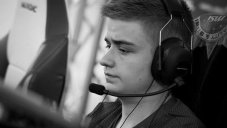
Features - Jul 10, 2023
5 Most Richest Esports Players of All Time
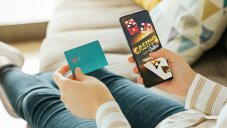
Features - Jun 07, 2023
Is it safe to use a debit card for online gambling?
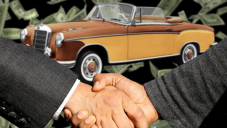
Features - May 20, 2023
Everything You Need to Know About the Wisconsin Car Bill of Sale
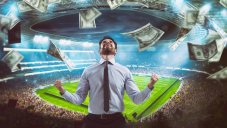
Features - Apr 27, 2023
How to Take Advantage of Guarantee Cashback in Online Bets
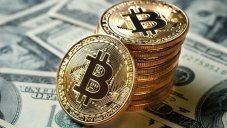
Features - Mar 08, 2023
White Label Solutions for Forex
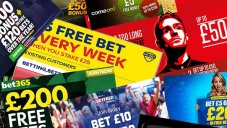
Review - Jul 15, 2022
WHY BETTING SIGNUP OFFERS ARE IMPORTANT FOR NEW GAMBLERS
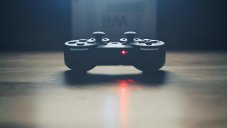
Mobile - Jul 01, 2022
The Best Sports Video Games to Play in 2022
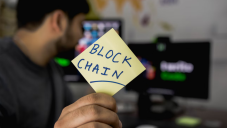
Features - Apr 28, 2022
0 Comments
Sort by Newest | Popular